PROJECTS IN 2017
LIQUEFYING SCRAP DOUGH / REWORK FOR CLIENTS EXISTING ARTISAN LINE FROM FRITSCH WITH OUT PARTNER BIOSTAR
BIOSTAR offers devices for production and dispensing of sour rye starter (sour rye starter tanks and plants), liquid rye sourdough with the yield of 190-200 (liquid rye sourdough tank), poolish (wheat sourdough tank), yeast milk (yeast fermentation tank) re-work processes (Scrap dough and baked products).
The system being the subject of the offer is designed for liquid rework processing. It can operate on many types of materials in batch: bread, pitta and pastry dough, pre-baked products and wastes from layering lines. Main idea of this process is to reduce bulk material waste and to improve the quality of the final products.
For liquefied rework system we propose line with cutting tank with 2 independent cutting agitators and storage tank with cooling system. The process will start from loading to the “cutting” tank waste dough or pre-baked material. On the control panel, the operator will establish how much rework material should be added to achieve optimum liquid rework yield (TA). The cutting tank will be placed on loading-cells, during filling the operator will be able to control weight loading of material. Next process step is destined for time refinement of liquefied rework. After adding water and old bread, the tank will start the mixing/cutting program. After this time material will stay in a mixing tank for time refinement (souring process). During this time, it will be possible to add from your existing fermentation system.
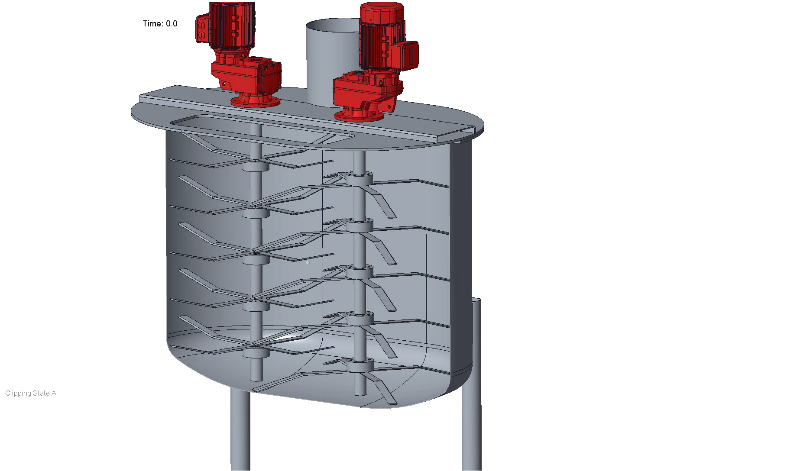
Short souring process is very important to keep liquefied rework safe from molds and strains. Fermentation process will also add to final product more moisture, volume, longer shelf-live and better taste, and aroma. After refinement time, liquefied rework will be pumped to storage tank by pump/emulsification stage and will be ready for dosing to the production line. The storage tank will be connected to the chiller which will reduce temperature of liquefied rework to 5oC. Dosing to the production will be realized by by-pass line to keep material in pipe in proper storage temperature.
How did this solution impact client’s business:
The reason for returns of dough is the profitability of production lines. Particularly interesting are dough recirculation systems in laminating or dough sheeting lines. Tracing scrap dough via belts into the extruder and inlet dough belt is the preferred and easy to implement with the existing technology. Sometimes, however, the scrap dough is so high (for example, with punched products), or the scrap dough is inherently so active that there are limits to the return because otherwise there will be too much quality variation over time.
At this point, solutions help in which the activity of the dough is made controllable. We would like to use as an example for an existing line. At present this line produce a lot of scrap dough which gets returned by belt direct to the Dough infeed belt towards the start of the line. At present this dough get mixed with the new dough which comes from the mixing station. See below picture.
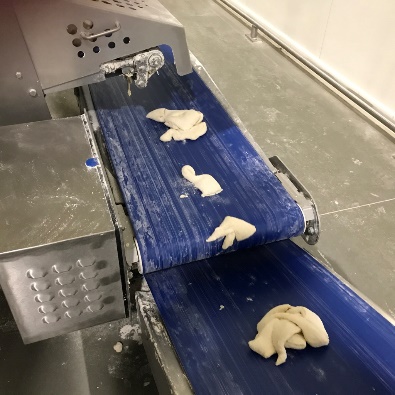
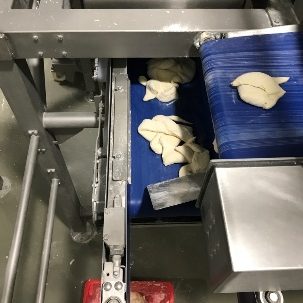
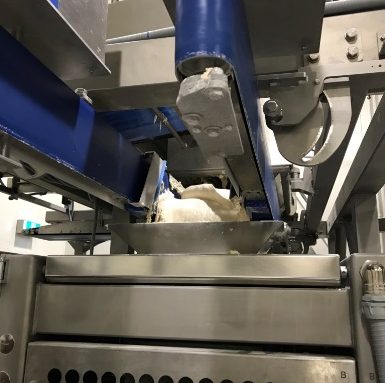
In this current process there is too much return of scrap dough towards new mixed dough. It has a bad dough quality which goes through the sheeter and the dough sheet does not run straight (line is not running as per set up).
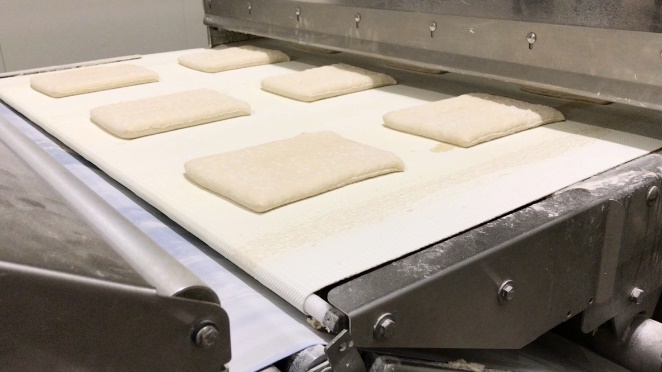
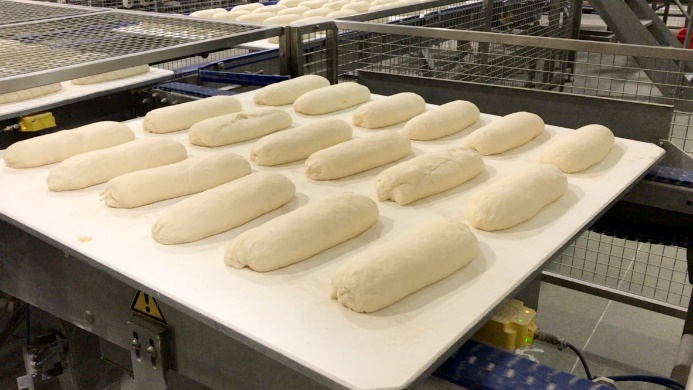
If scrap dough gets liquified it gets a better consistency of the dough structure and there is less dough wastage. The weight of final dough pieces after cutting can be controlled much better and the final product gets a better quality.
FULLY AUTOMATIC SLICING, PACKING AND CLOSING SYSTEM WITH A CAPACITY OF 3000 PIECES PER HOUR FOR GLUTEN FREE LOAVES & BUNS WITH OUR PARTNER HOBA
Examples:
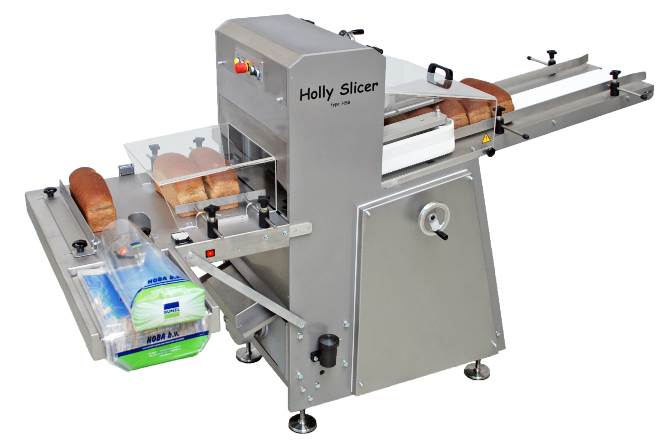
HOLLY SLICER TYPE HSB
The Holly Slicer has reciprocating blade and is constructed for manual use or in combination with an automatic packing line Holly Bag Loader. The products infeed with bottom and side belts, these side belts are adjustable by handwheel. The standard comes with outfeed guide plate and side guides after the slicing section with photocell control for the sliced products at the end to stop the feeding. It is suitable for wet loaves or with ingredients like raisins or fruit.
HOLLY FLOW PACKER HFP 75
The Holly Flow Packer has quick replaceable plastic rear pushers suitable for food use and is made by three sets of fin wheels: the first set diameter 120 mm, is cold, tilt able and used to drive the film, the second one, diameter 120 mm, is heated, used to weld the film, whilst the third set, diameter 120 mm, is cold, used to drive the film; film cooling air blow. The first set of wheels open through touch screen and the products are loaded from the left side and discharged to the right.
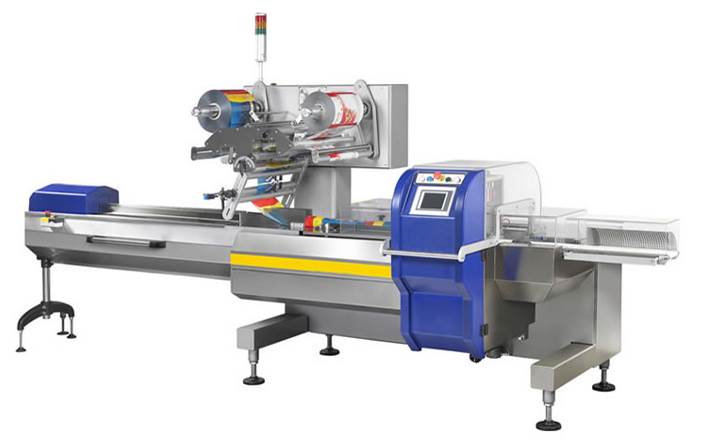
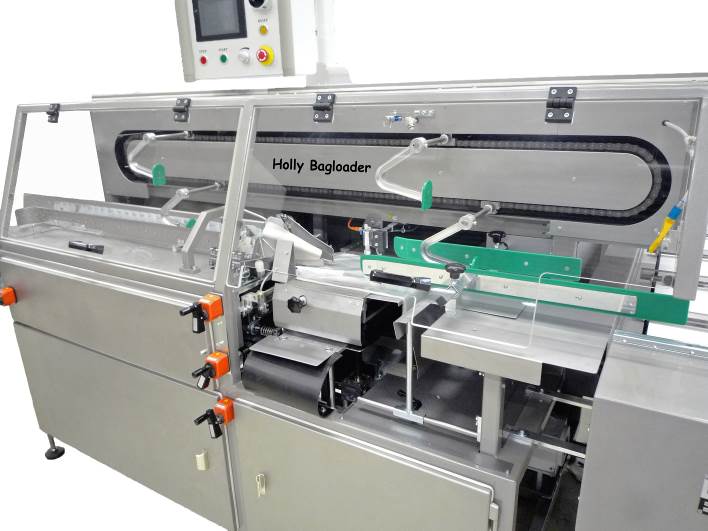
HOLLY BAG LOADER TYPE HBS
The model HBS comes with a four-pusher system and can be connected with the Holly Slicer and Holly Packing Line. It is developed to pack various unsliced and sliced bread, as well as buns and rolls. The Holly Bag Loader is available in left- or right-hand version. A photocell controls for the last bag and whether the bag is opened or not. The bag table height is regulated automatically by a motor drive.
HOLLY PACKAGING LINE TYPE HTA-KL
This model has a continuous working conveyor and is also suitable for combination with a bag loader or flowpackmachine. The products are transported with pushers on a plastic plate. It is a solid built and easy to operate machine with practically no maintenance.
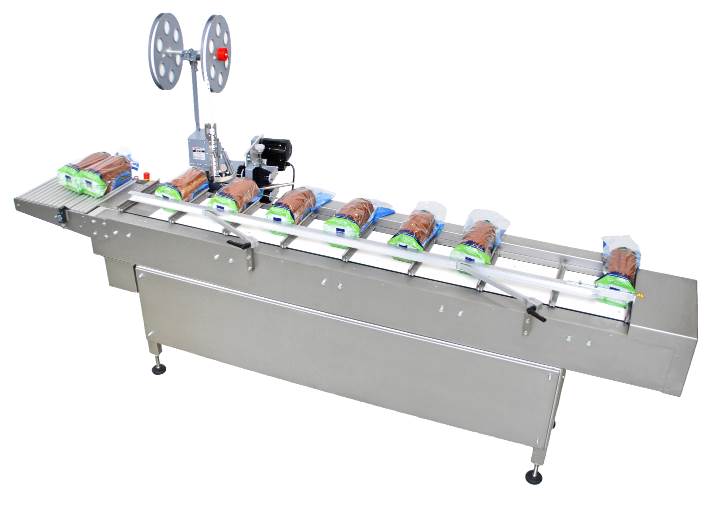
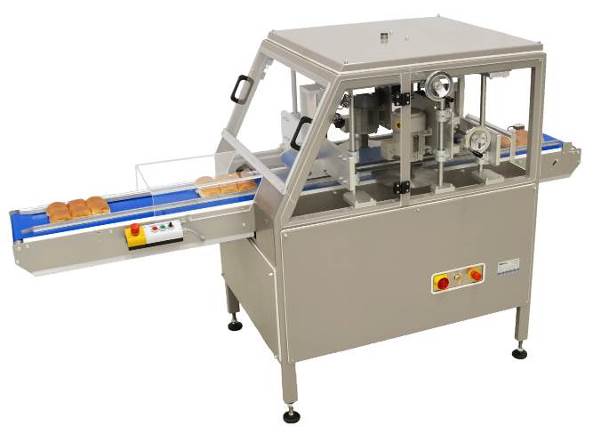
HOLLY BUN SLICER TYPE HSC
This model comes with four circle discs to make on two lines butterfly cut. The product are sliced horizontal. The Holly Bun Slicer has a double stopper system to make row of the products, so when 4 complete, a signal is given to the stopper. The products are checked by photocell control. This type of slicer is constructed for manual operation in combination with a cooling conveyor system or automatic packing line.
HOLLY FLOW PACKER TYPE HFP 50
The Holly Flow Packer is a horizontal flow pack system for packing of different types of products. It has a longitudinal sealing unit, made by three sets of fin wheels diameter: first set is cold and used to drive the film whilst the second one is heated used to weld the film and the third one is cold and used to drive the film, film cooling air blow.
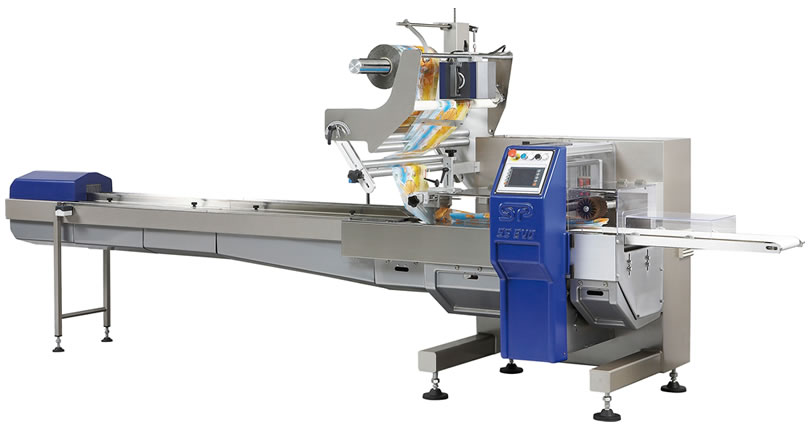
REPLACE LONG MOULDER STATION OF EXISTING FULL AUTOMATIC PRODUCTION LOAF WITH A NEW LONG MOULDER STATION OF OUR PARTNER GOSTOL
We from TARGET Hospitality built in cooperation with our client a new moulding station in synchronization with existing plant. The top belt of second long roller will be driven and a proper loading of products towards the trays is given. The long moulder can synchronize and integrate with existing tin transport system.
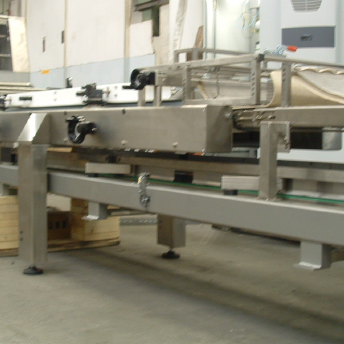
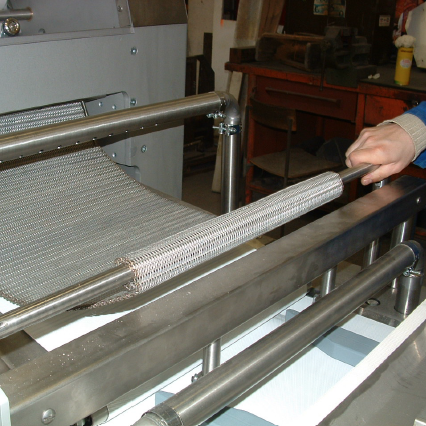
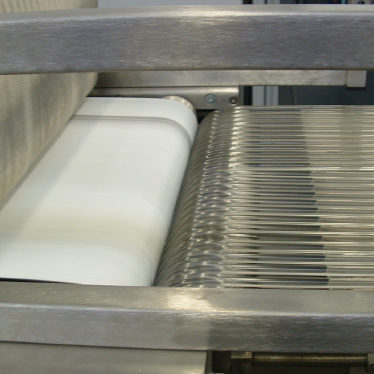
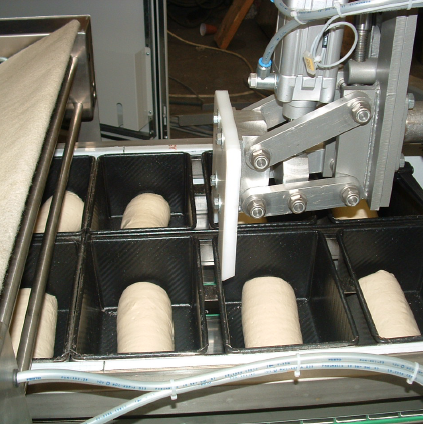
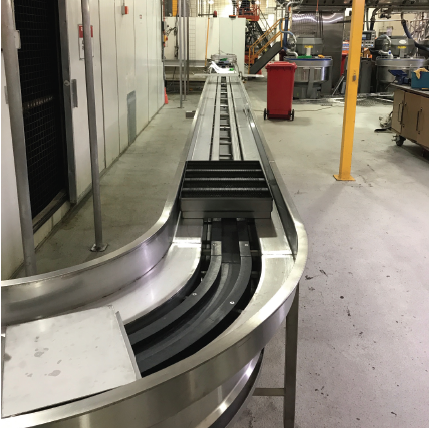
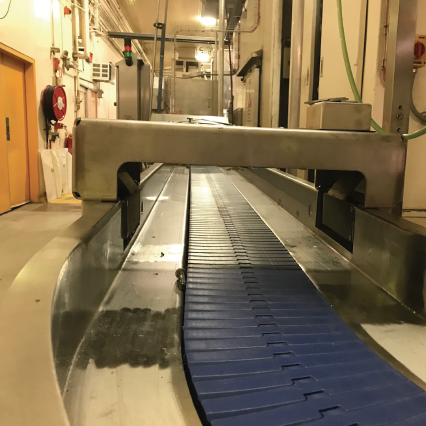
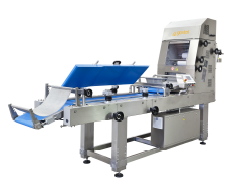
The long moulder type SORA is designed for moulding of wheaten dough loaves. Due to its high production output and sturdy construction is the perfect final moulder to be employed in larger industrial bread production plants.
After cutting, the dough pieces are separating on belts conveyor. The distance between two pieces is adjustable.
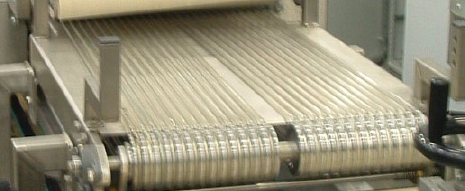